The Apache helicopter has long been the Army’s alpha dog. It’s designed to find, fix, and, if necessary, target the adversary to support ground troops and/or Joint Force Commander.
But it takes an incredible amount of situational awareness for pilots to complete these missions.
That’s where our radar and sensors come in.
Modernized Target Acquisition Designation Sight/Pilot Night Vision Sensor (M-TADS/PNVS) systems provide Apache pilots enhanced situational awareness and greater performance and survivability.
We maintain these sensor systems, known as the “Eyes of the Apache”, so that they are sustainable for the warfighter for years to come. But how do you ensure that level of readiness for the customer? Through successful execution of Performance Based Logistics (PBL).
Supply Parts and Services Quickly
Since its inception in 2007, our Performance Based Logistics team ensures that Apache aircrews always have what they need to keep flying. We provide sensor upgrades and maintenance at all major Apache sites, repair facilities and forward operating bases.
That includes the Lockheed Martin Missiles and Fire Control Depot Support Facility (DSF), which has over 47,000 square feet of storage and supply chain logistics space – including nine automated vertical storage systems.
Averaging 1,200 shipments per month, the DSF is the National Inventory Control Point that provides spare parts and repair unit management to supply and repair centers supporting the Apache Fire Control (AFC) program throughout the world.
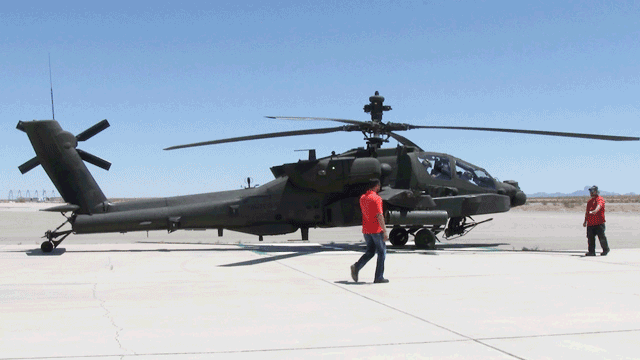
Ensure Maintainability
The Apache helicopter and the sensors that outfit it continue to evolve to keep up with an everchanging threat environment. As this evolution occurs, our service engineers adapt to new software, hardware, and test equipment to provide long-term support to our customers.
Our renowned field service engineers travel on-site to provide education and tools to operators and maintainers. This ensures repairs and upgrades are managed correctly, minimizing costly re-work.
Reduce Lifecycle Support Cost
Long-term affordability is key to helping our customers stay at-the-ready.
Development and procurement traditionally account for about 20-30% of a product’s total ownership cost, while costs to operate, maintain and dispose of it account for about 70-80% of the total.
PBL is more than a simple repair and return program—it’s a proactive engineering services program that focuses on system and logistics improvements, lowering total lifecycle costs.
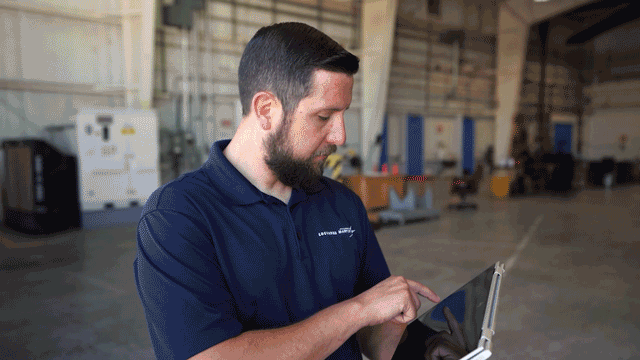
Advanced Training Processes
To ensure Apache Pilots are ready to go when the mission calls, PBL gives us the advantage to find innovative ways to increase efficiency in how we train and support our customers.
RELY3D is a prime example. RELY3D is an interactive suite of applications that supports Apache aircraft maintainers with M-TADS/PNVS virtual guides, 3-D animations, wiring diagrams and more. It offers interactive training and features that support the reduction of maintenance time on the Apache M-TADS/PNVS system.